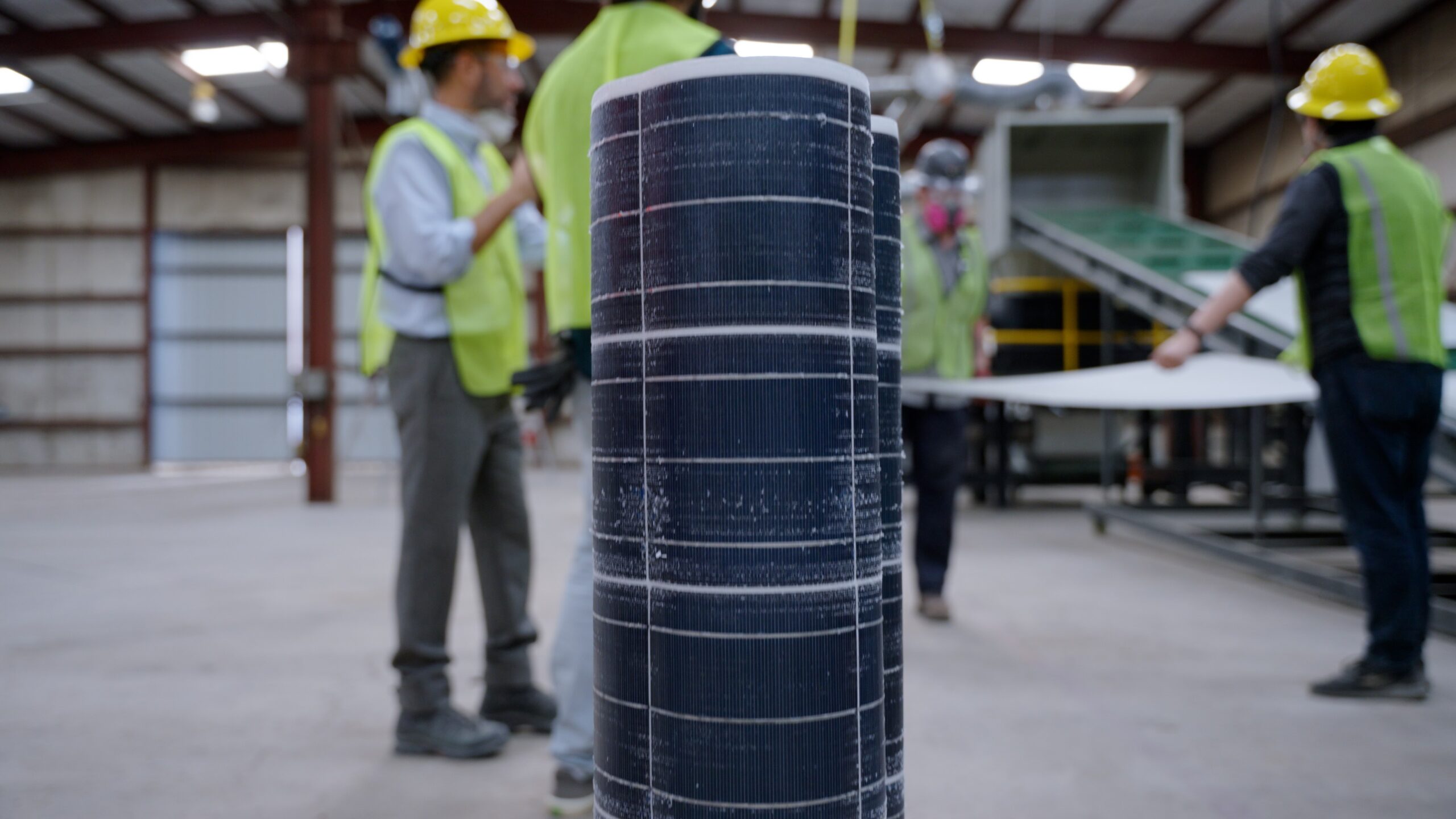
DEPCOM and its industry partners explored how to achieve solar industry circularity effectively and responsibly during a webinar called “Turning Solar Panel Recycling Woes into Industry Wins.” Co-sponsored by the Solar Energy Industry Association (SEIA), the webinar featured DEPCOM EVP John Schroeder alongside SOLARCYCLE,TM CEO Cofounder Suvi Sharma, and Silicon Ranch CEO and Cofounder Reagan Farr discussing such issues as solar asset longevity, creating value streams, and community stewardship. Here are some key takeaways from the experts.
Why think “circular?”
Rapidly expanding solar capacity is a critical part of any renewable portfolio designed to reduce emissions. But developing a sustainable infrastructure requires thinking holistically — in a circular way — to avoid creating new problems.
Passage of the Inflation Reduction Act inevitably will lead to more and more solar PV deployment. In their Solar Market Insights report, Wood Mackenzie and SEIA note that the industry is building toward average annual growth of 21%. But over the next 25 years, this deployment boom ultimately will result in end-of-life (EOL) waste that must be considered now.
Strategic planning now provides an opportunity to consider how to recover valuable materials from PV modules and perhaps even reuse many of them. Some in the solar industry already have begun to realize this opportunity and are proactively building a circular and sustainably scalable market.
How do we extend the lifetime of solar panels?
Long-term thinking is key to extending PV system lifetimes, something that draws keen interest from solar asset owners vested in the reliability and longevity of their equipment. When such assets reach their end of life, plans need to be in place for what happens next.
Creating well-designed decommissioning and recycling plans from the start lowers overall project risks, improving the financial prospects over the asset’s life.
In addition to the inherent aging of equipment, EOL issues also can crop up in relation to warranty returns, scrap materials from manufacturing activities, damage from weather events, and operational issues. DEPCOM’s services include planning for restoration and major maintenance overhauls.
Shifting the industry’s mind-set to a long-term perspective is key to sustainable practices. Such a mindset requires refurbishing equipment even long after a manufacturer goes out of business, which requires designing with backward compatibility in mind. For example, if an extreme weather event damages a project’s panels, designers need to plan for the possibility that replacement panels may not be compatible with the existing system.
How do solar panels get recycled?
Logistics management and optimization make up the first steps in recycling solar panels. SOLARCYCLE partners with large-scale solar asset owners to manage all of their end-of-life needs under long-term recycling service agreements. The company optimizes panel packaging and transportation to maximize the number of panels each truck can carry, saving costs and lowering a project’s overall carbon footprint.
The next step in solar panel recycling involves thinking about how to reverse-engineer, or “un-manufacture,” these panels to find the best way to extract valuable materials at high volume with a focus on zero-waste. First, the frames are separated using a mechanical process. Next, the glass — which accounts for 70% to 90% of the panel’s weight — is removed. The remaining components, a combination of metal and plastic, then are crushed and shredded into small pellets, which can be separated into discrete metals and plastics using a combination of electricity and gravity.
There are a number of manufacturers interested in purchasing and reusing the separated materials. Things like aluminum, silver, copper, and especially glass are highly prized; solar glass has a low iron content that is available only in limited quantities as a raw material in the U.S. That makes the recycled glass all the more valuable. “We don’t just want to extract materials and get value,” Sharma explained. “We also want to create value by developing new solar glass rather than selling it to bottling companies.” At the same time, however, he noted that plastics are fundamental to the durability and longevity of solar panels, but are more challenging to recycle. SOLARCYCLE is working with materials companies to downcycle plastics from solar panels into filler materials to add them back into the value chain.
All of these processes are automated, which is key to driving costs down. Not including freight charges, factory recycling costs range from $10 to $15 per panel. This premium is due in part to the limited amount of waste, the scarcity of recyclers, and the long distances, and thus high logistics costs, involved in transporting modules to recycling facilities. Still, the cost of recycling compared to the overall cost of decommissioning is small. Advances in technology and achieving better economies of scale can bring the premium down to roughly $5 per panel. Over time, the most value in solar panel recycling will come from rendering out the raw materials, rather than just the recycling fees.
How do we move forward with a circular economy for the solar industry?
Creating a circular economy requires identifying appropriate recyclers. To that end, SEIA has created a National PV Recycling Program to develop a network of vetted recyclers capable of reusing, reselling, and refurbishing solar materials. A circular solar economy also offers additional features:
1) Thinking about community stewardship
Reagan Farr with Silicon Ranch extolled the virtues of community stewardship, including developing a clear narrative around the positive aspects of transitioning to sustainable energy sources. Designers now are building in regenerative land management and dual-use between agriculture and solar panels. Farr urged a similar mindset shift toward modules that are past their useful life. Everyone wins when the industry can demonstrate its capabilities as good long-term community partners.
2) Establishing true chains of custody
EOL decommissioning plans should require engineer/expert certification. Even if the developer is not in business as the module ages out, the component nonetheless would be recycled. Creating a seal of approval affirming that a facility is committed to recycling, panelists said, could streamline a community’s acceptance at the project’s genesis. SEIA is uniquely positioned to create such a stamp of approval and vet recycling companies.
3) Preferring recycled content
One effective way to support circularity in the industry would be for solar panel buyers to prefer products with recycled content that still meet safety and performance requirements with competitive economics. This could result in a robust recycling market, increasing volume and driving costs lower.
4) Defining responsibilities from the start
Panelists agreed that developing standard EOL operating procedures is a critical part of creating a circular solar economy. Designating a project EOL principal at the outset would ensure that the end of life is taken into consideration from a project’s beginning moment.
For solar to scale to its fullest potential, the experts agreed, it needs to create a vibrant secondary market for used panels and recycled materials. Responsible solutions can prove to be both ecologically sound and economically responsible.