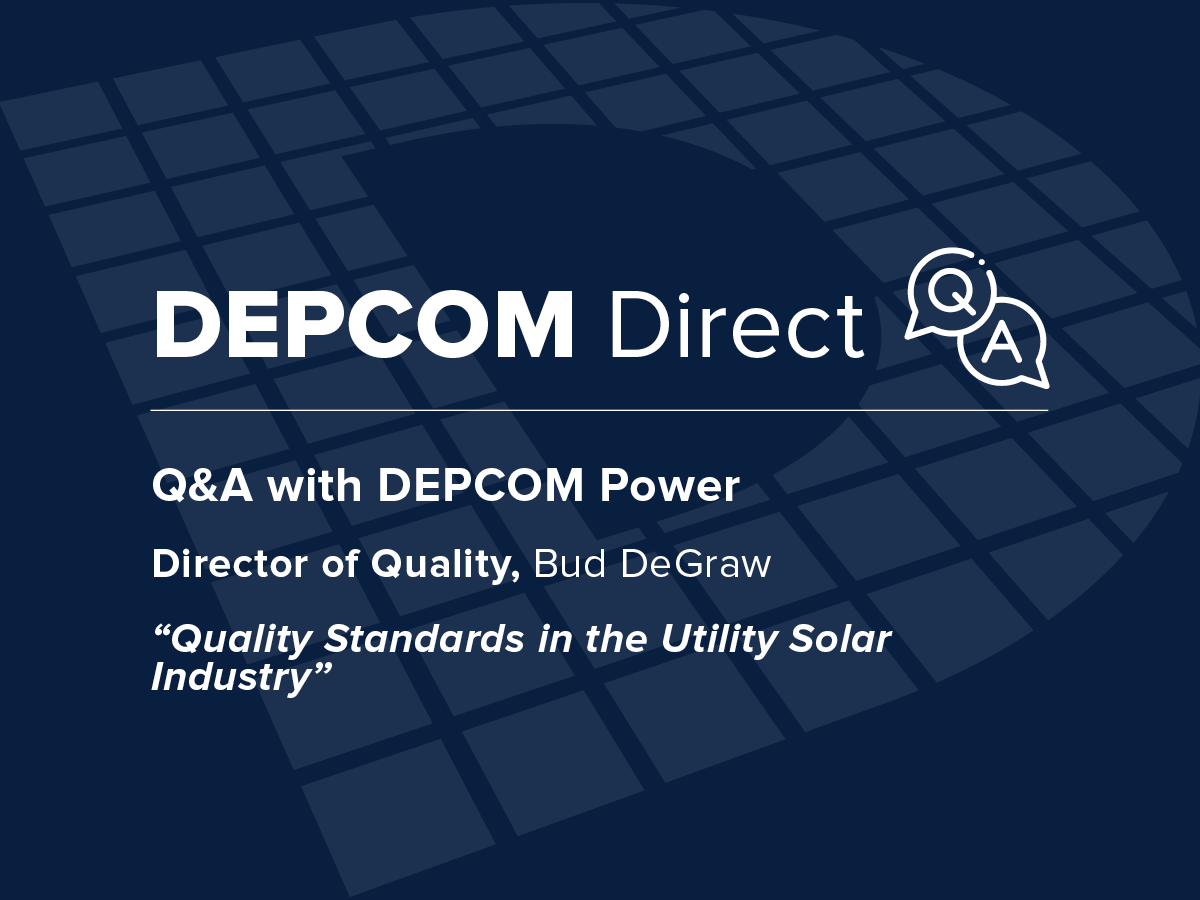
DEPCOM’s Director of Quality, Bud DeGraw, talks about the culture of Quality at DEPCOM Power and how the industry can uphold high standards amidst its booming growth.
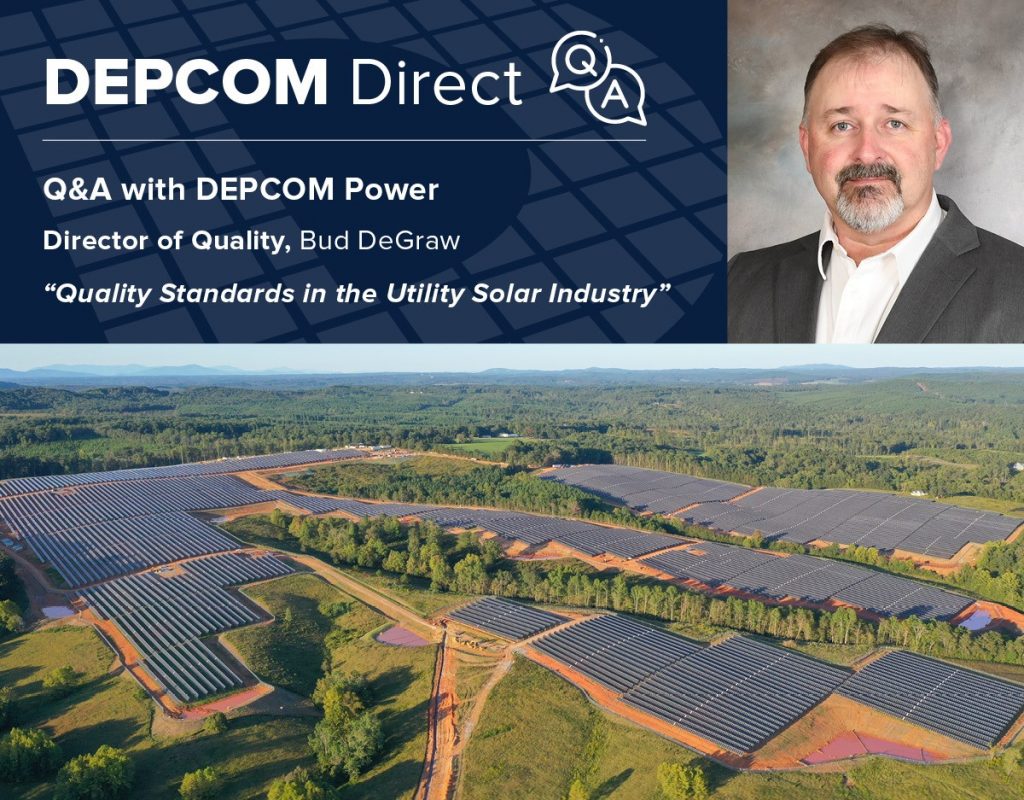
Q: What does a typical day look like as a Quality Control ( QC) Manager at a DEPCOM utility solar site?
A: A day at a DEPCOM site begins with the morning construction meeting where Safety, Quality, Construction, and Project Managers coordinate site-wide priorities and initiatives. Action items each day are determined using maps and engineering drawings in combination with input from personnel in the field, and then prioritized. Every QA/QC agenda, every sampling rate, and every quality measure is documented with the highest scrutiny to ensure that accurate data is communicated internally and externally to customers.
Q: How do DEPCOM quality measures go above and beyond industry standards?
A: DEPCOM performs some of the highest sampling rates seen in the construction industry and is held to the most stringent of quality standards. Setting the bar high for quality sampling rates gives the field team more actionable data to track time sensitive issues and gives the advantage of identifying non-conformities earlier in a process which saves the entire team time.
Using LEAN principles, DEPCOM’s QA/QC team has also developed internal processes like our unique torque wrench calibration testing and labeling program. To ensure that no uncalibrated wrench makes its way on site, every torque wrench is tested to ISO standards, their serial number documented and DEPCOM’s visual labeling system applied. These types of DEPCOM specialized Quality Control processes are what sets DEPCOM up to excel in increasingly challenging sites across the country.
Q: What types of unique technologies are used for QC on DEPCOM sites?
A:The field utilization of software in conjunction with tablets allows personnel to quickly inspect, identify, and report progress in the field. These progress reports are generated to be used internally and are also sent externally so construction progress metrics can be tracked by customers in parallel with Quality Supervisors.
In addition to employing the top market technologies, DEPCOM fosters innovation and is currently migrating to an in-house software program designed by one of DEPCOM’s own project managers. This new customizable software is built to showcase lessons learned, turning that information into actionable, company-wide logistical data that can be applied on the field and in the office. DEPCOM team members are continually creating process improvements and this culture of innovation helps us stay ahead of the curve.
Q: How have you built a Quality culture at DEPCOM?
A: Everyone here at DEPCOM takes unbelievable pride in everything they do, and it starts with the top-down directive of building “National Championship” teams. Be it logistics, contracts, engineering, administration and of course construction, everyone takes personal pride and accountability for producing the best product possible. From personal experience, the most effective way to engrain quality is through peer leadership training. DEPCOM’s Quality Leader program is led by on site Quality Control personnel to conduct Quality orientation training to Mechanical Superintendents, Quality Technicians and Crew leaders to emphasize the standards of DEPCOM’s commitment to quality. Trained individuals are then able to become certified Quality Leaders themselves to train additional personnel resulting in leadership development for DEPCOM’s entire team.
Q: DEPCOM designs and builds large megawatt projects that span thousands of acres. What advice would you give to other QC professionals in the industry on how to manage that scale of scope of utility solar project?
A: Staying focused on perfecting the fundamentals, proactive engagement and communication is how DEPCOM builds success on all projects. Our Quality Managers are actively engaged with Pre-Construction, Engineering, and Site Managers to ensure quality is prioritized at every phase of construction and maintenance. Routine communication sessions with our customers builds a mutually beneficial relationship for general progress reports and instant feedback to solve any project roadblocks.
Q: What do you forsee to be the challenges QC management will face as the future of utility solar projects looks to include more challenging build environments?
A: From a QA/QC perspective, the greatest challenge is maintaining clear and actionable communication within dynamic and ever-changing site conditions, from site prep to final commissioning. At DEPCOM, we are addressing the expanding project scope size by ensuring our quality processes are scalable, and continuously reinforcing the value of personal pride in every task.